PLCs vs. Industrial PCs: Key Difference Explained
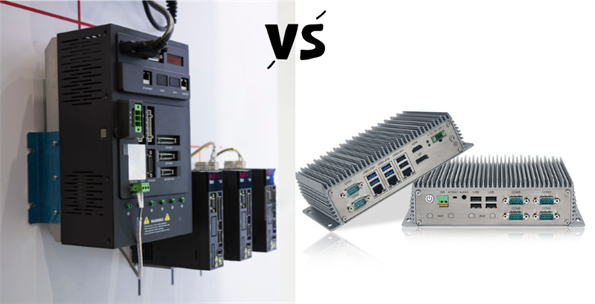
As industries continue to embrace digital transformation, the need for robust, reliable, and flexible automation technologies becomes increasingly critical. With advancements in both PLCs and IPCs, businesses are faced with a myriad of choices that can significantly impact their operational capabilities. This article aims to delve into the nuances of PLCs and IPCs, highlighting their distinct features, strengths, and ideal use cases.
What Is A PLC?
Programmable Logic Controllers, or PLCs, are specialized computers used to control manufacturing processes. They are reliable, durable, and specifically designed to withstand harsh industrial environments. Originating from the automotive industry, PLCs have evolved to become a staple in various sectors, including manufacturing, energy, and logistics.
The Basics of PLC Technology
PLCs are the backbone of many industrial automation systems. They are built to be resilient and are typically used for repetitive tasks like assembly line operations, where reliability and uptime are critical. Their architecture is optimized for executing pre-defined sequences of operations, ensuring precise control over machinery and processes.
PLCs are programmed using ladder logic, a graphical programming language that resembles electrical relay logic diagrams. This makes them particularly intuitive for engineers and technicians who have a background in electrical engineering. Furthermore, ladder logic's simplicity aids in troubleshooting and maintaining the systems, reducing the time required for repairs and adjustments.
Advantages of PLCs
- • Robustness: PLCs are designed to handle extreme conditions, including temperature fluctuations, dust, and vibrations. This robustness ensures that they continue to operate effectively even in the most challenging environments, minimizing the risk of failure.
- • Reliability: Known for their long life and minimal downtime, PLCs ensure continuous operation. Their design prioritizes stability, which is crucial for maintaining production schedules and reducing unplanned stoppages.
- • Real-time Performance: They can execute tasks in real-time with high-speed processing, which is crucial for time-sensitive applications. This capability is essential for processes where timing precision directly impacts product quality and operational efficiency.
- • Ease of Use: With straightforward programming and maintenance, PLCs are user-friendly for those familiar with automation tasks. Their intuitive interface allows for quick updates and modifications, facilitating rapid responses to changing production requirements.
Applications of PLCs
PLCs are predominantly used in applications that require precise control and automation. Common applications include:
- • Assembly lines: PLCs manage the sequential operations of assembly lines, ensuring products move through each stage efficiently and accurately.
- • Conveyor systems: They control the speed and direction of conveyors, optimizing material flow and reducing bottlenecks.
- • Robotic devices: PLCs provide the precise control needed for robotic arms and devices in various manufacturing processes, enhancing productivity and precision.
- • Safety control systems: They monitor and manage safety protocols, ensuring compliance with industry standards and safeguarding personnel and equipment.
What Is An Industrial PC?
Industrial PCs are more general-purpose computing devices that offer flexibility and computational power. They are used in applications where complex computations, data storage, and networking are needed. As industries grow more data-driven, IPCs play a vital role in harnessing and analyzing large volumes of information.
The Basics of Industrial PCs
Industrial PCs are similar to regular PCs but are built to withstand industrial conditions. They are typically used in applications requiring high data processing capabilities, like data acquisition, machine vision, and human-machine interfaces (HMIs). IPCs are equipped with robust hardware components designed to endure the rigors of industrial settings, ensuring longevity and performance.
Unlike PLCs, IPCs support multiple programming languages, which makes them adaptable for various tasks and industries. This flexibility allows developers to utilize advanced programming techniques and tools, tailoring solutions to specific industrial challenges and enhancing overall system capabilities.
Advantages of Industrial PCs
- • Flexibility: IPCs can run a wide range of software applications and support multiple programming languages, making them versatile. This versatility enables businesses to customize their systems to meet diverse operational needs and accommodate future technological advancements.
- • High Processing Power: They offer superior computational power, making them ideal for complex tasks that require significant data processing. This capability allows IPCs to handle sophisticated algorithms and simulations, supporting innovation and efficiency improvements.
- • Integration Capabilities: IPCs can easily integrate with other systems, allowing seamless data exchange and communication. Their connectivity features facilitate the creation of interconnected environments, promoting efficient collaboration and data sharing across different platforms.
- • User Interface: With advanced graphics capabilities, IPCs provide sophisticated interfaces for operators and engineers. These interfaces enhance user experience, enabling intuitive interaction with complex systems and improving decision-making through detailed visual representations.
Applications of Industrial PCs
Industrial PCs are versatile and used in diverse applications that require advanced computing and data processing. These include:
- • Process control systems: IPCs manage complex process variables, optimizing production efficiency and product quality.
- • Data acquisition and analysis: They collect and analyze vast amounts of data, providing insights that drive operational improvements and predictive maintenance strategies.
- • Machine vision systems: IPCs process high-resolution images and video streams, enabling defect detection, quality control, and automated inspection processes.
- • Advanced HMI (Human-Machine Interface) applications: They offer intuitive interfaces for operators, improving interaction with complex systems and enhancing overall user experience.
Key Differences Between PLCs and Industrial PCs
To choose between a PLC and an IPC, it's essential to understand their fundamental differences. These differences are not only technical but also pertain to the operational philosophies they embody.
Application Suitability
PLCs: Best for repetitive, time-critical tasks in harsh environments. Ideal for controlling machinery and processes that require high reliability. Their deterministic nature ensures that operations proceed without delays, essential for maintaining production line consistency.
IPCs: Suitable for applications that need extensive data processing, complex calculations, and sophisticated user interfaces. They excel in environments where data-driven insights and real-time analytics are crucial for operational success.
Programming and Flexibility
PLCs: Use ladder logic, which is limited but straightforward for certain tasks. Less flexibility in terms of programming languages. This limitation makes PLCs ideal for scenarios where simplicity and reliability are prioritized over versatility.
IPCs: Support multiple programming languages, offering greater flexibility and the ability to handle diverse tasks. Their adaptability makes them suitable for evolving industrial landscapes where rapid technological changes are common.
Cost Considerations
PLCs: Generally more cost-effective for simple automation tasks. The cost of ownership is lower due to their reliability and minimal maintenance needs. Their predictability in performance and upkeep makes them a financially sound choice for many operations.
IPCs: Higher initial costs due to their advanced capabilities and processing power. However, they provide value in applications requiring complex computations and integrations. The potential for significant ROI in data-rich environments justifies their investment for many businesses.
Environment and Durability
PLCs: Designed for extreme industrial conditions, ensuring longevity and reliability. Their rugged construction makes them a staple in industries where environmental challenges are a daily occurrence.
IPCs: Although robust, they are more suitable for controlled environments and may require additional protection in harsh settings. Their need for supplementary safeguarding can introduce additional considerations for deployment in certain applications.
Choosing the Right Technology for Your Needs
When deciding between PLCs and IPCs, consider the following factors. Each factor plays a crucial role in determining which technology aligns best with your operational goals and constraints.
- • Nature of the Task: Determine whether your application requires simple control tasks or complex data processing. Understanding the core requirements of your operations will guide you towards the most appropriate technology.
- • Environment: Assess the conditions where the system will operate. PLCs are better for harsh environments, while IPCs suit cleaner, controlled settings. Environmental compatibility is key to ensuring longevity and performance.
- • Budget: Consider both initial costs and long-term maintenance expenses. PLCs offer cost-efficiency for basic tasks, while IPCs provide value for complex applications. Analyzing total cost of ownership will help in making a financially viable decision.
- • Integration Needs: If your system requires integration with other IT systems or advanced user interfaces, IPCs may be the better choice. Their connectivity and adaptability make them ideal for integrated, modern industrial ecosystems.
InnoAioT: Your Trusted Industrial PC Manufacturer
InnoAioT delivers a comprehensive range of industrial PCs engineered to meet the demands of modern industrial automation. With over a decade of industry expertise, our team designs and manufactures robust, high-performance computer systems built for the toughest industrial environments. Every InnoAioT system is purpose-built, rigorously tested, and field-proven to ensure long-term reliability and performance. Whether you're upgrading your factory, building a smart city solution, or powering mission-critical applications, InnoAioT is your dependable partner for industrial computing. Contact us today to discover how our industrial PCs can support your innovation.